Bronze Casting
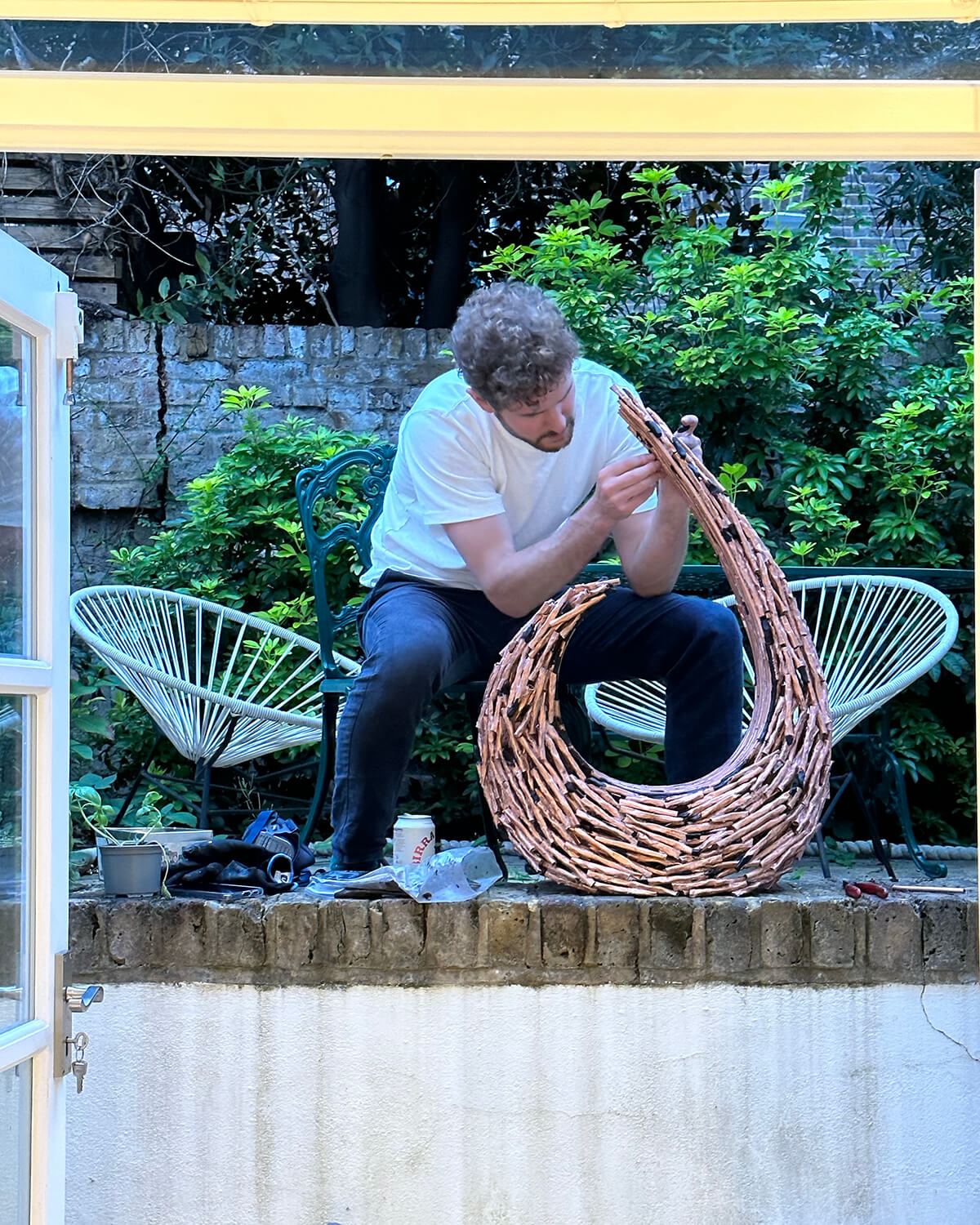
1. Create the original sculpture, which in my case is created from reclaimed metals.
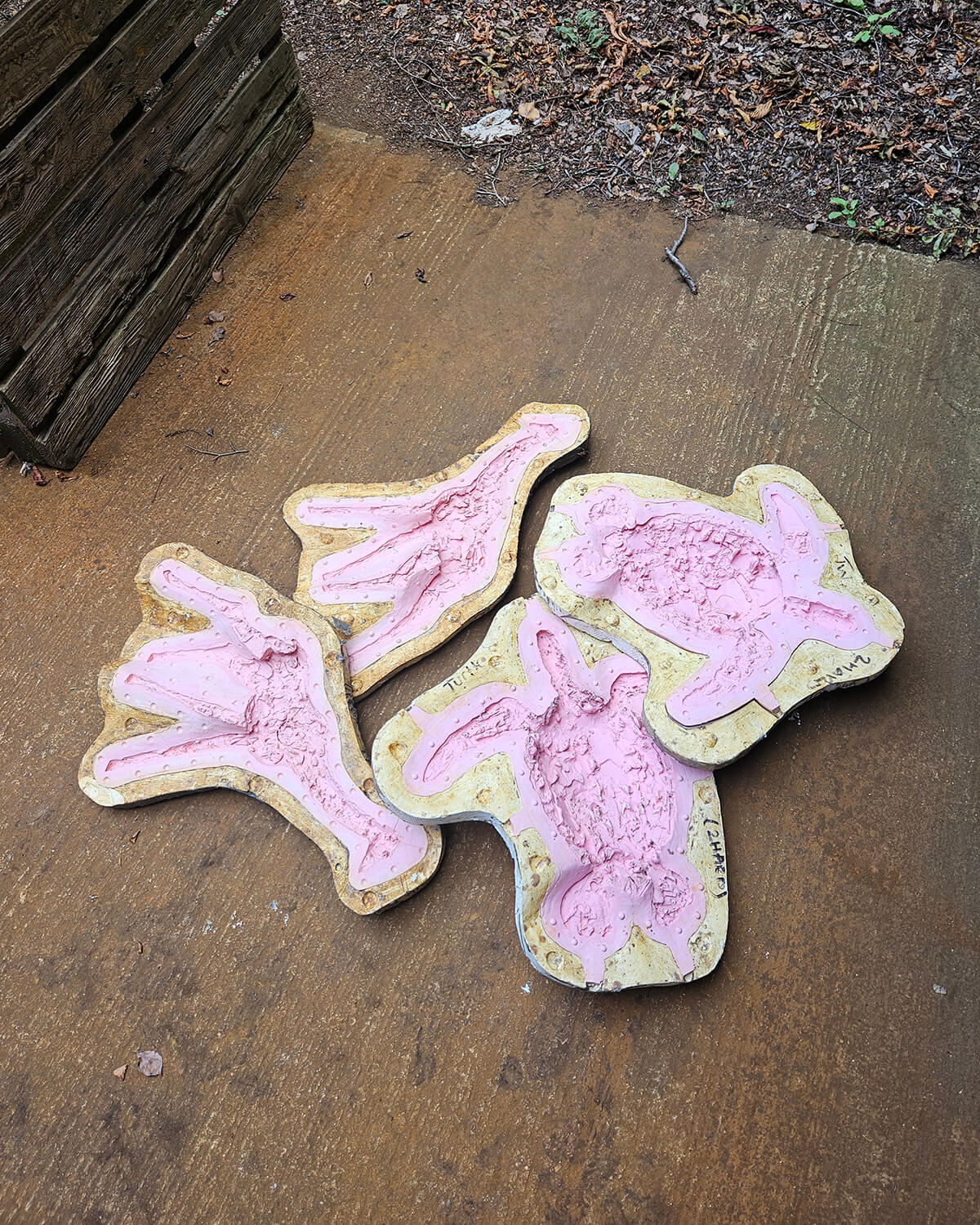
2. Make a mold, which is a flexible rubber mold that is created from the original sculpture to capture all details.
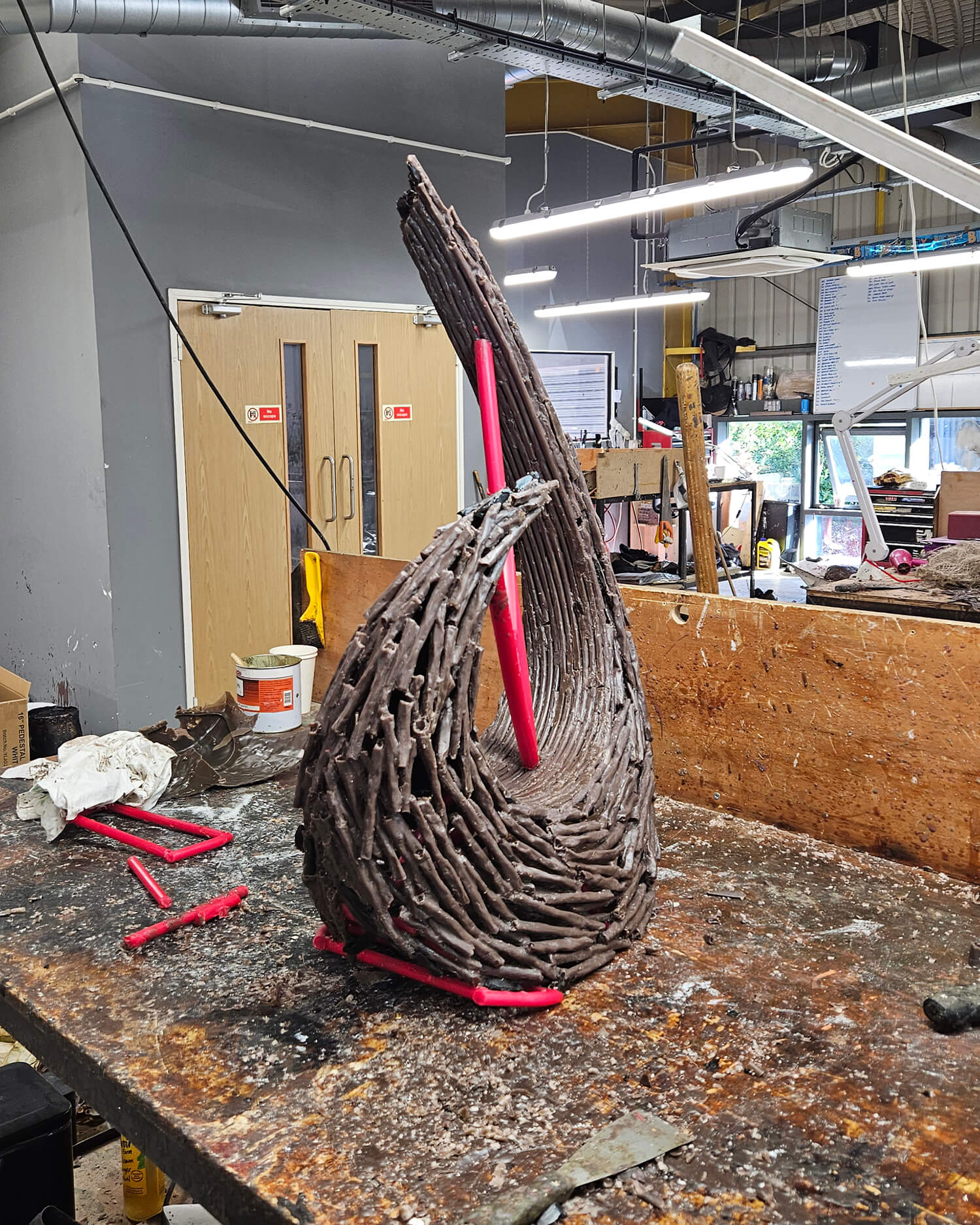
3. Create a wax replica, by pouring molten wax into the mold to create an exact wax copy of the original sculpture.
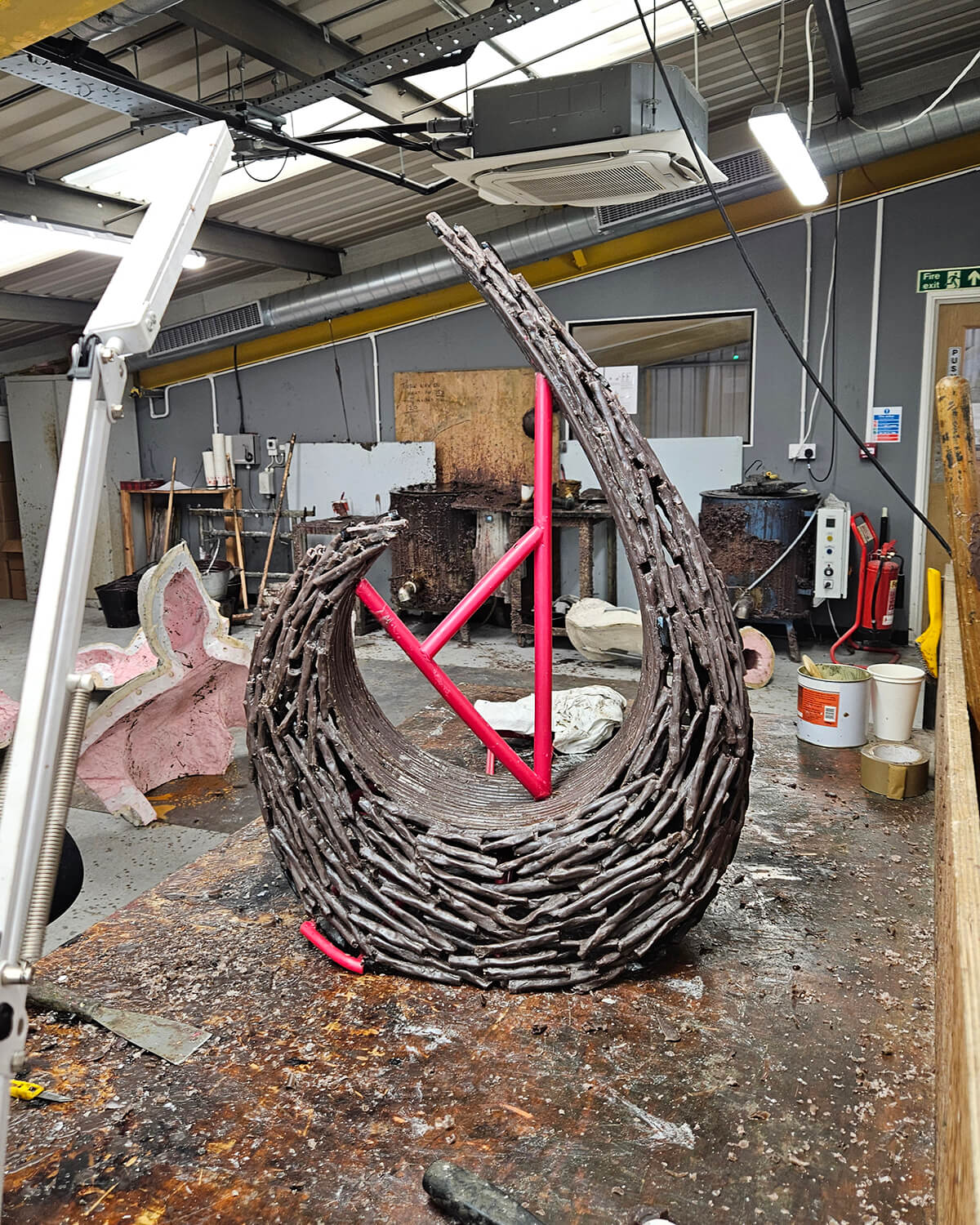
4. Attach wax sprues and vents, which create channels for bronze to flow in and air to escape.
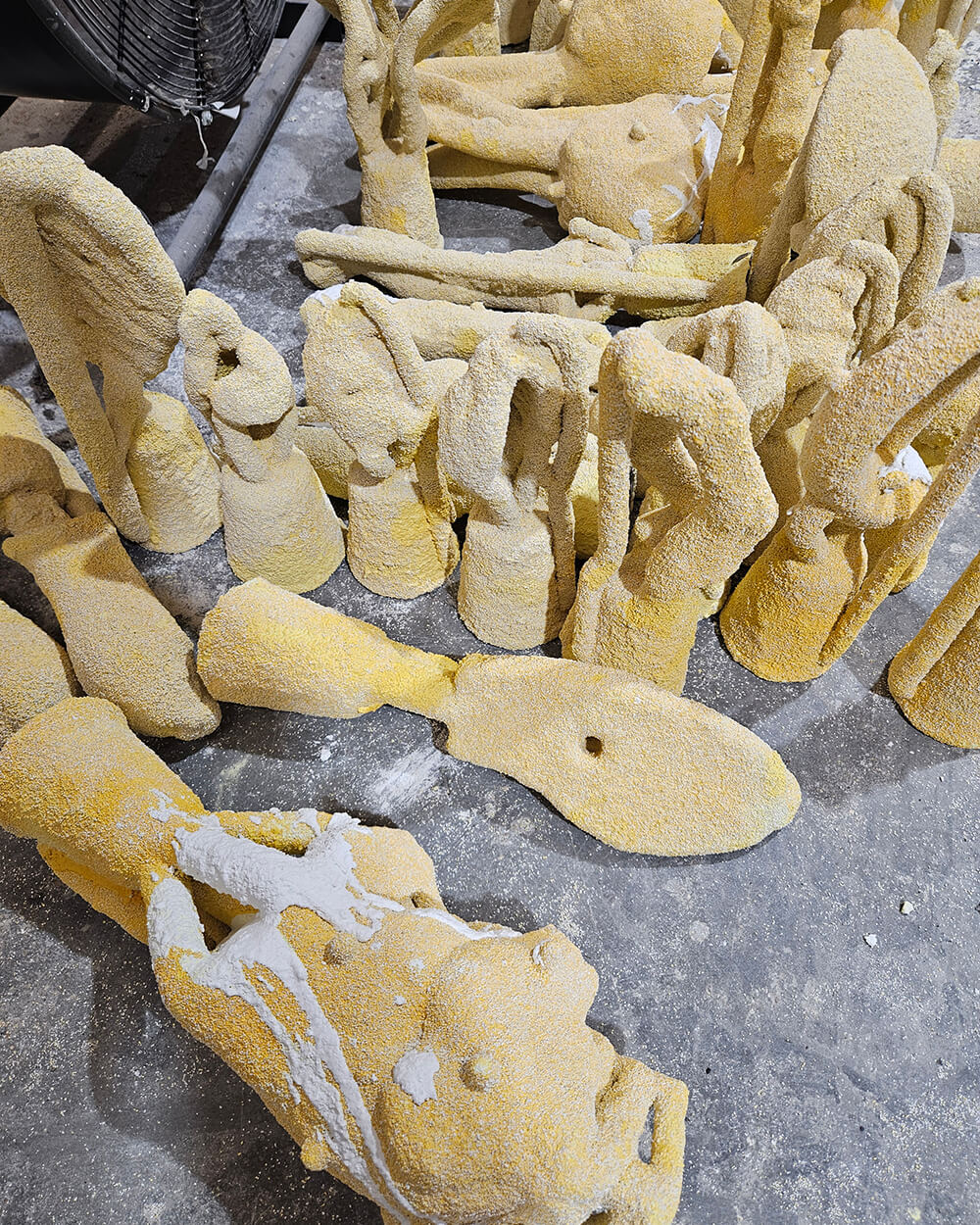
5. Create the ceramic shell, by dipping the wax replica repeatedly in ceramic slurry and coating with silica sand to build up layers.
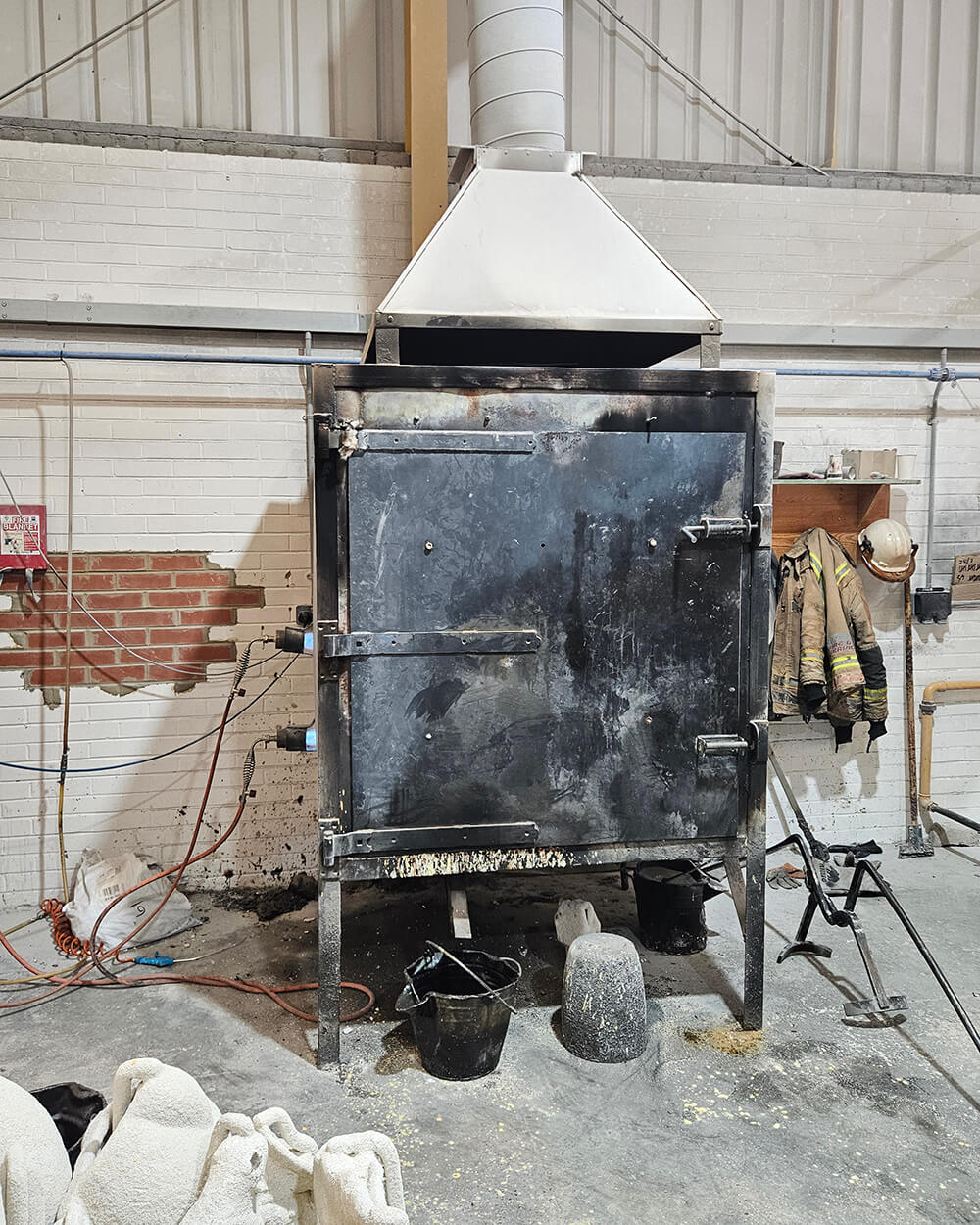
6. Melt out the wax, by heating the ceramic coated wax replica in a kiln, which melts and drains the wax, leaving a hollow mold.
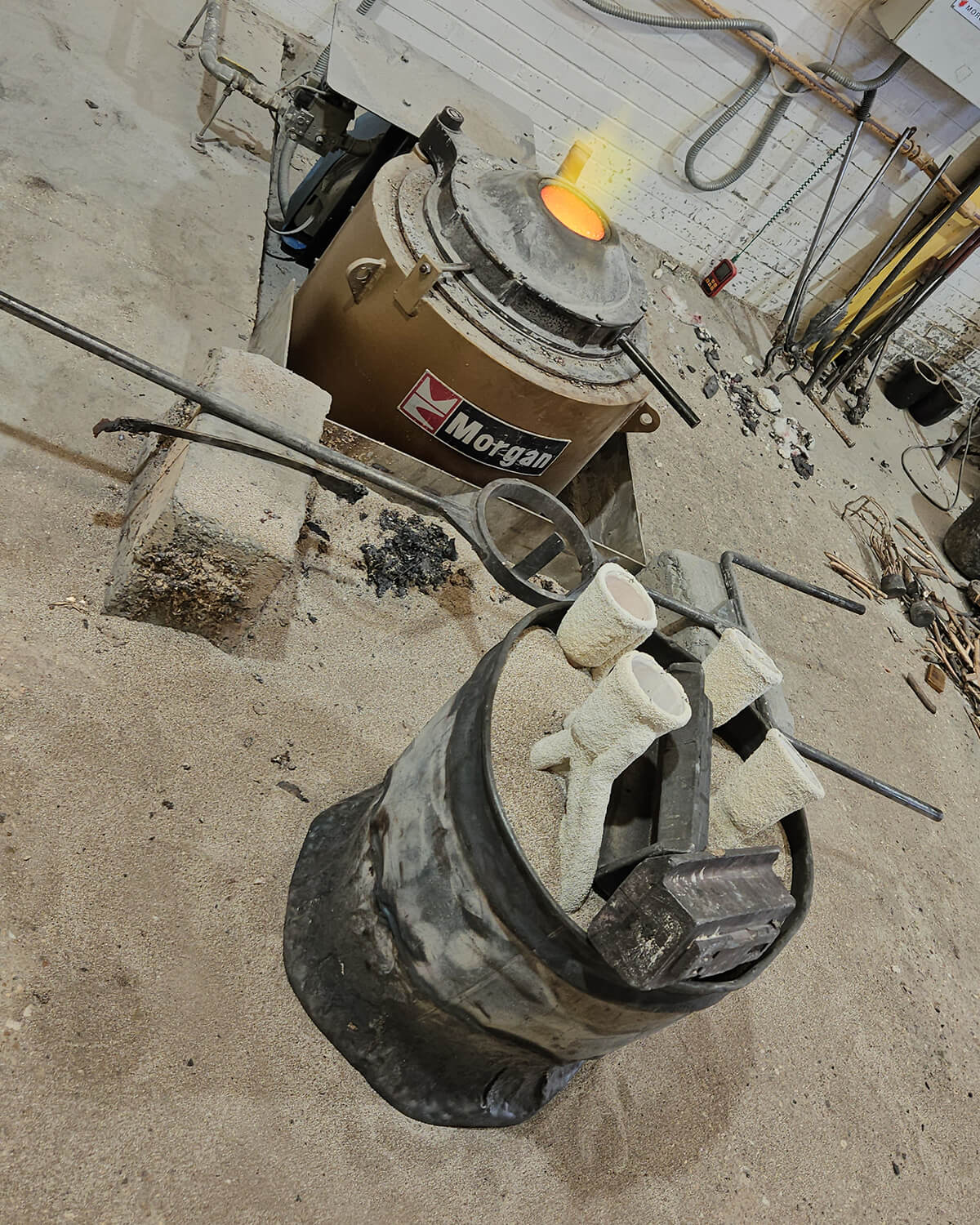
7. Pour the molten bronze into the heated ceramic mold, filling the void left by the wax.
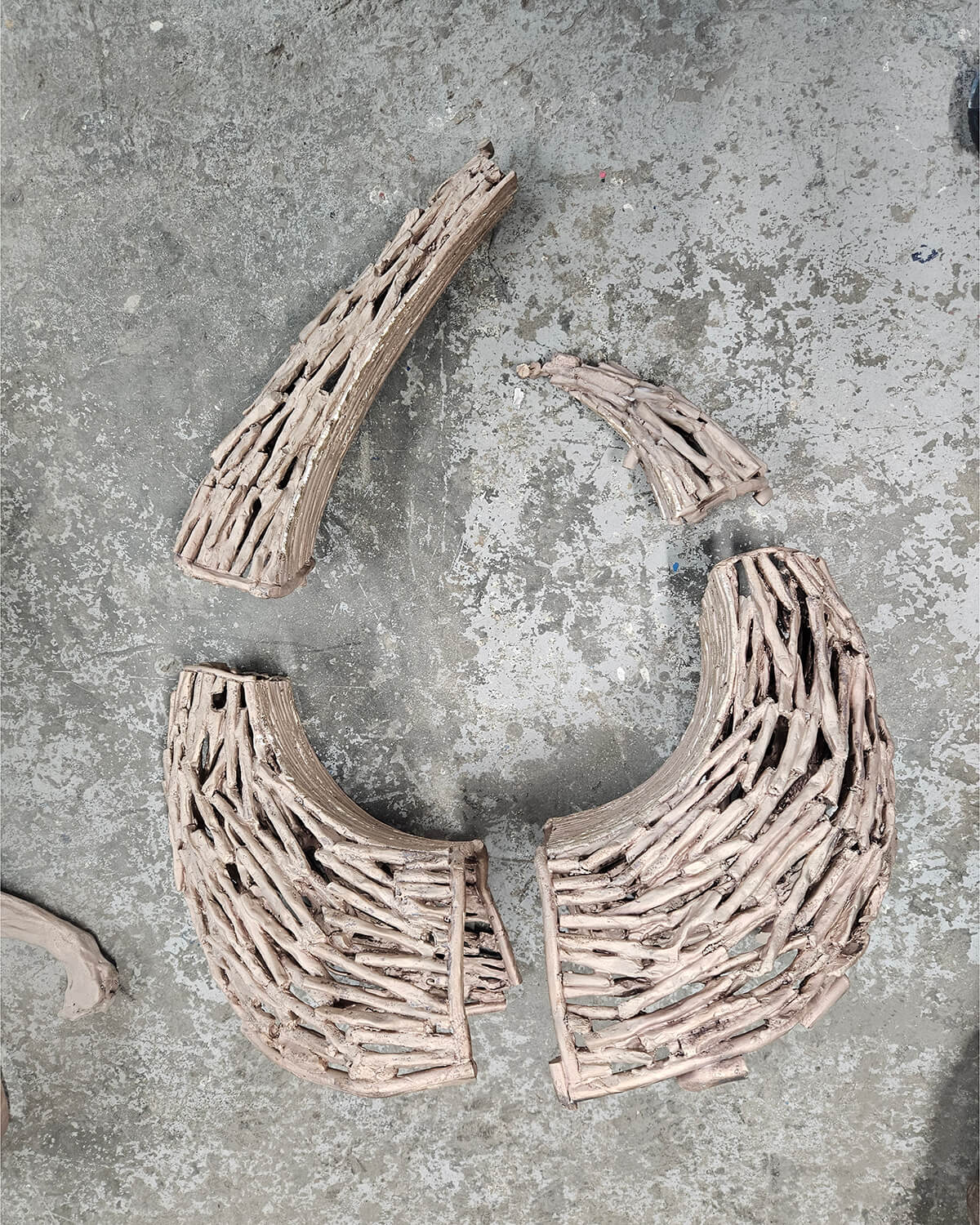
8. Break the ceramic shell and cut off sprues and vents. Once cooled, the ceramic shell is carefully broken away to reveal the bronze casting. The bronze channels created by the wax sprues and vents are cut off the sculpture.
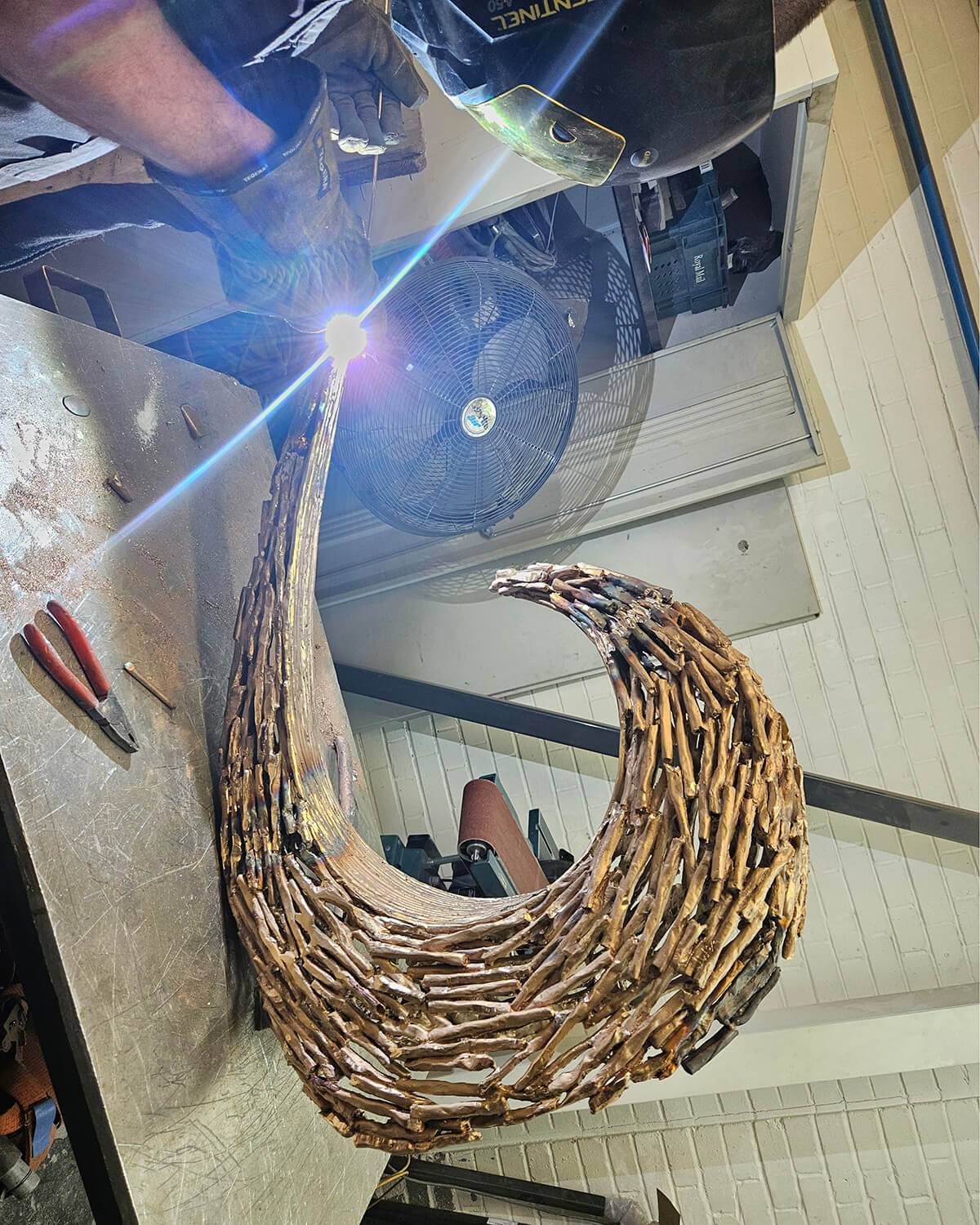
9. Weld and chase the sculpture, to ensure that the bronze replica of the original sculpture is correct.
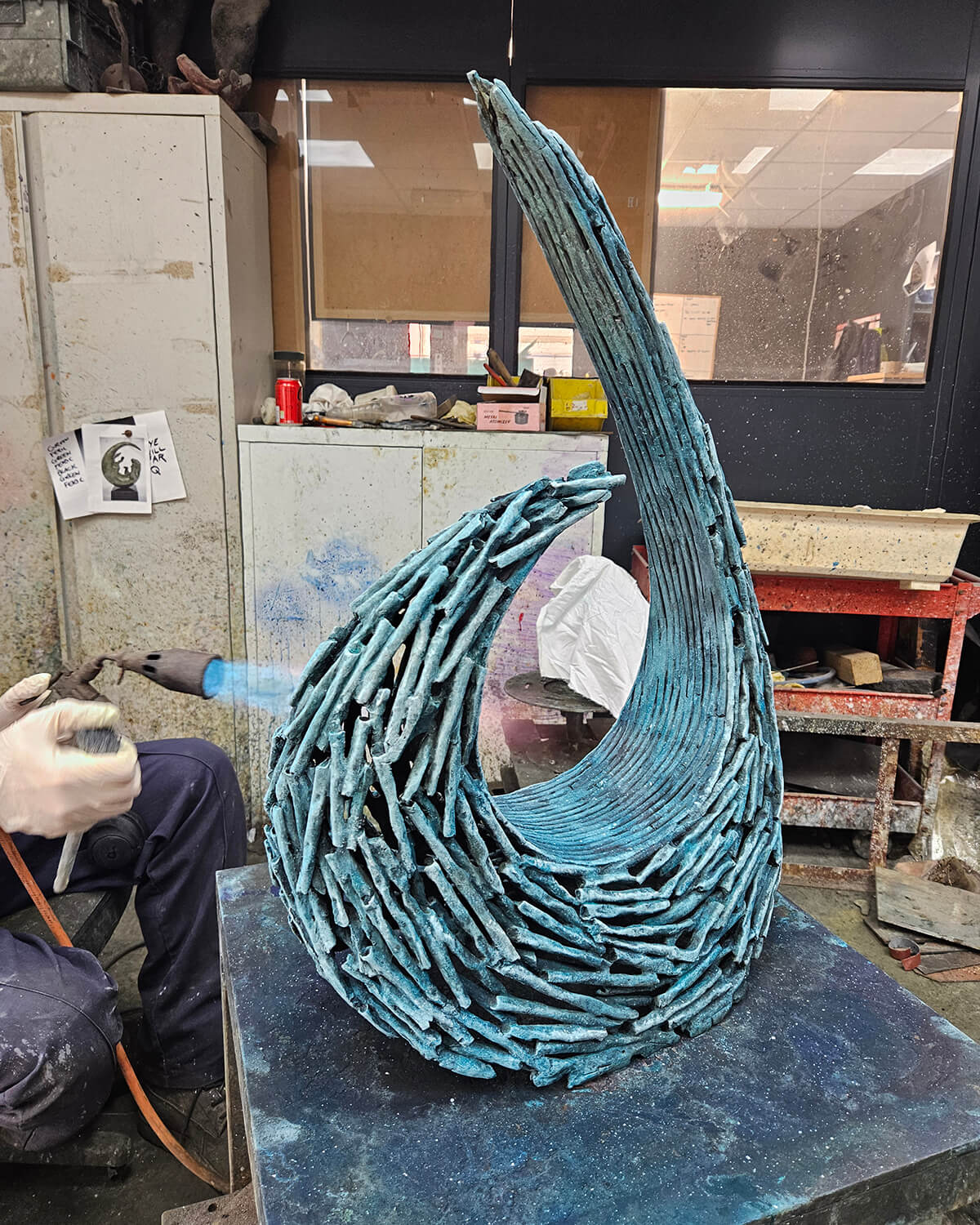
10. Apply patination and finishing, during which the bronze is cleaned, any imperfections are repaired, and a patina is applied for color and protection.